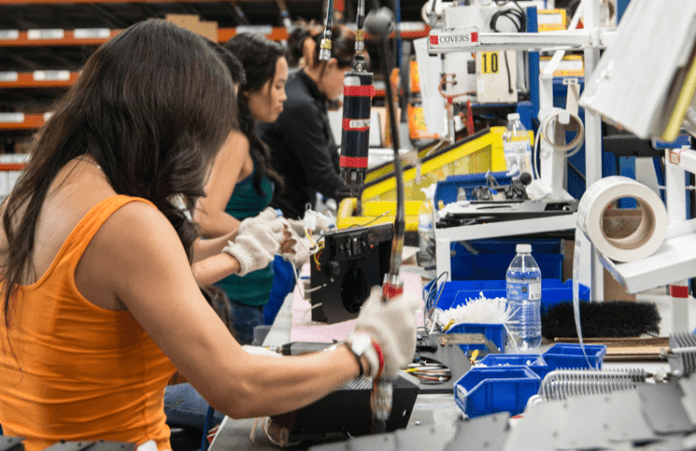
The manufacturing industry in Clark County and the Greater Portland area may look relatively small and stable right now, but economic developers see a boom looming just around the corner.
That could be great news, but it comes with a problem: There aren’t enough workers in the area right now to fill the upcoming needs of the growing industry. About a fifth of the Greater Portland’s manufacturing workforce is set to retire in the next few years, and fewer young people are training for manufacturing careers in school. And that’s left industry leaders worried about how to fill the gap.
In response, a coalition of 20 companies and a handful of economic development groups, including the Columbia-Willamette Workforce Collaborative and Workforce Southwest Washington, recently launched a new website and campaign to encourage students to look more closely at manufacturing careers.
“One of the biggest things I think is needed is really showing students the value of these careers,” said Mike Bomar, president of the Columbia River Economic Development Council (CREDC), which is a sponsor of the site. “If you just look at jobs right now, I think you’re missing the bigger picture for manufacturing. The industry is poised to grow.”
The site, www.CareersNW.org/Manufacturing, provides information about wages, the broad range of industry jobs, day-in-the-life videos, an interactive display of what local companies make, and links to training and support. It’s modeled after the well-trafficked WorkSource site for the healthcare industry, which was launched a few years ago.
“We modeled this after that idea, which was successful,” said Cass Parker, Workforce Southwest Washington’s senior industry initiative manager. “After it launched, they had a lot of people visiting the (healthcare) site, they had a successful job fair out of it and that site still exists.”
Manufacturing is one of four major focus areas for a collaboration of economic development groups in the six-county area around Greater Portland. The other areas are healthcare, high tech and clean tech. The area includes Clark, Cowlitz and Wahkiakum counties in Washington; and Clackamas, Multnomah and Washington counties in Oregon.
Clark County had about 13,600 manufacturing workers in 2016, or 8.8 percent of the overall county workforce. That number stayed about the same in 2017. There used to be a lot more manufacturing jobs in the area, but offshoring and the economic downturn in 2000 shrunk the industry. In 2000, there were 17,300 manufacturing workers in Clark County, Bomar said.
“We’re just starting to get back to pre-recession levels,” Bomar said. “We’ve seen it hit bottom and slowly crawl up, with the jobs being different, but the industry still being important.”
The projected need for manufacturing workers in the county is 20,300 by 2020 and 20,900 by 2025.
Industry has changed in recent years
So, where’s that growth coming from? The industry has changed quite a bit from its line production days. Today, automation and computer programming are driving a lot of production. And workers need some different skills to compete. But with an average wage of $44,650 a year, retraining and picking up some of those skills can be highly rewarding, Bomar said.
“There’s new equipment, new technologies online that make it safer for workers, but there’s a learning curve,” Bomar said. “Employees need to understand mechanical workings, but they also need some coding.”
There are also some areas of the industry where workers are constantly in demand, such as welding, Parker said.
“We could probably fill welding positions all day, every day,” she said. “It’s a very specific skill. It requires certifications, but it’s not a long process. People don’t know about welding and they don’t know it’s actually a great paying job. You can get a certificate at a community college and get started quickly.”
The problem is, students – especially in K-12 – aren’t being exposed to what the modern day industry is like, or what careers are available, Bomar said.
“One of the big challenges was the demand side,” Bomar said. “There’s a disconnect on value and opportunities, and students are unclear on the advantages.”
That’s something Parker has seen as well.
“Younger people aren’t being exposed to manufacturing in school,” Parker said. “They tend to be more focused on becoming doctors, lawyers, schoolteachers, and don’t consider that manufacturing has changed a lot.”
And that’s one of the main reasons the group decided to create the new website. It has a wide array of information about jobs in the industry, what skills are needed, where to find educational help and which companies are hiring.
“At the end of the day if we get people into family wage jobs, while meeting the needs of the business community, it’s going to create more economic opportunity,” Parker said.
Completing/funding THE NEW WEB site
The manufacturing site took about a year to complete and cost somewhere between $100,000 and $110,000 to build. About $50,000 of that came from manufacturing companies and economic development groups. The rest is covered through co-investment with private partners, Parker said.
“The rest of the money came from a variety of different funding streams,” Parker said. “We now have money designated for messaging. That’s a bit of a new concept for us.”
The manufacturing site, and the prior site on healthcare, are a bit of a new trend for economic developers in the region. It’s likely that the group will also develop websites in the future to reach out to potential workers in the other two focus areas – high tech and clean tech, Parker said.
“We realized the way we can meet our strategic goals is that we do everything with a sector focus now,” Parker said. “We’re skilling up our staff to better understand the sectors.”